Hooray! I am now on holidays and have lots of time to work on my boat!
I have glued on the keel and the two inside battens.
The taper on the keel was achieved by routing slots at the appropriate depths. The resulting 'staircase' was then smoothed to a taper with a hand plane.
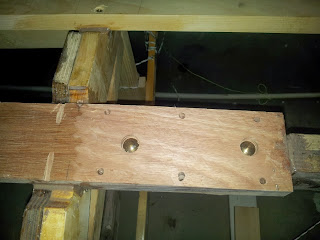.jpg) |
Keel and batten epoxied in place. |
The chines are the next challenge to work on. It turns out that they are not quite as simple as I first imagined. (like a lot of things in life I suppose).
I started off by bending the chine in the approximate position and cutting/filing the notch on frame 2 to suit the curve of the chine. A small block was epoxyed in place to fill a gap. Sharp chisels are really useful for this kind of work I have found.
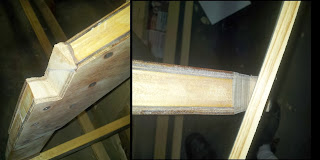 |
Notches before and after. (Photos show opposite sides of the boat) |
The tricky part of the chine is determining the correct amount of twist between frame 2 and the stem. If there is to little twist, there will not be a sufficient angle on the chine to point towards the sheer. As shown in the picture below, if the chine is rotated anticlockwise, the side planking will no longer fit. If the chine is rotated clockwise, there will be a point at which the bottom planking will not fit. It is a very fine balance especially near the stem. When you have it right in one place, it is wrong in another etc......
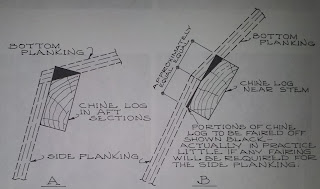.jpg) |
Correct alignment of the chine. It looks simple in 2D. Much more complex in curving 3D! |
Another point that I had to consider is that the extension of the line of the chine should end at the middle of the stem.
THERE ARE SO MANY THINGS TO CONSIDER!!
I spent so long pondering them and trying to get it right that I am now convinced that it is nearly impossible on the Squirt to twist the chine enough to have it meet the sheer.
I have decided to just do what everyone else does and add a tapered piece of wood to the chine after it is glued in place.
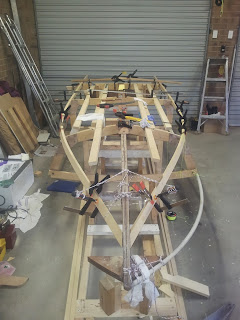.jpg) |
Chines held in place with rope and clamps |
Laminating the chine before making the final adjustments to the chine-stem junction seemed to be a good idea so that is what I did. It was relatively easy to do. I put a layer of epoxy on each lamination before applying thickened epoxy as the glue.
Put the chines together, clamp them up, clean up the epoxy and its done.
Plastic was used at the frames and stem to stop the chine gluing to them.
As I am sure every boat builder has exclaimed a multitude of times, 'YOU CAN NEVER HAVE TOO MANY CLAMPS!' I have spent $225 on clamps so far!
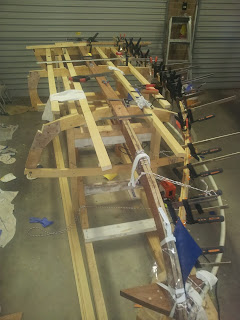.jpg) |
Chines being laminated |
There should be time to get started on the sheers in my 2 weeks of holidays. For this reason, I have set up a soaking pipe to soak the sheers in. I am really not sure how well the sheers will bend because they are a lot fatter than the chines and don't look to keen on bending! Hoop Pine apparently doesn't respond to steaming either. If I break a sheer, I think I will just get more wood and go for 3 laminations.
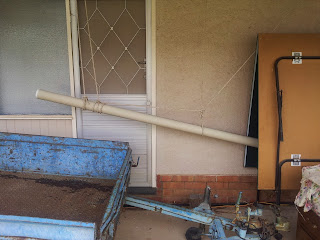.jpg) |
Water pipe for soaking sheers |
I am enjoying your blog very much.
ReplyDeleteI have this week received my Squirt plans, I am building the Squirt for my Year 12 Project, so I have only 8 months part time to complete (yep, a big challenge). Jet power is my current choice.
I am located in Warburton, east of Melbourne. I noticed you are in Aus maybe we could communicate a little.
Regards
Jude