Summer is over :-( but the boat building is not :-)
I was determined to get the bottom plywood planking on before I go away at Easter time.
As of today, I have half the bottom planking glued on!
The plywood bottom planking had been scarf jointed before my last post. The first step in regards to getting the bottom planking installed, was to cut the panels roughly to size. The planking was laid on the boat, rough marked to approximate size, and trimmed accordingly.
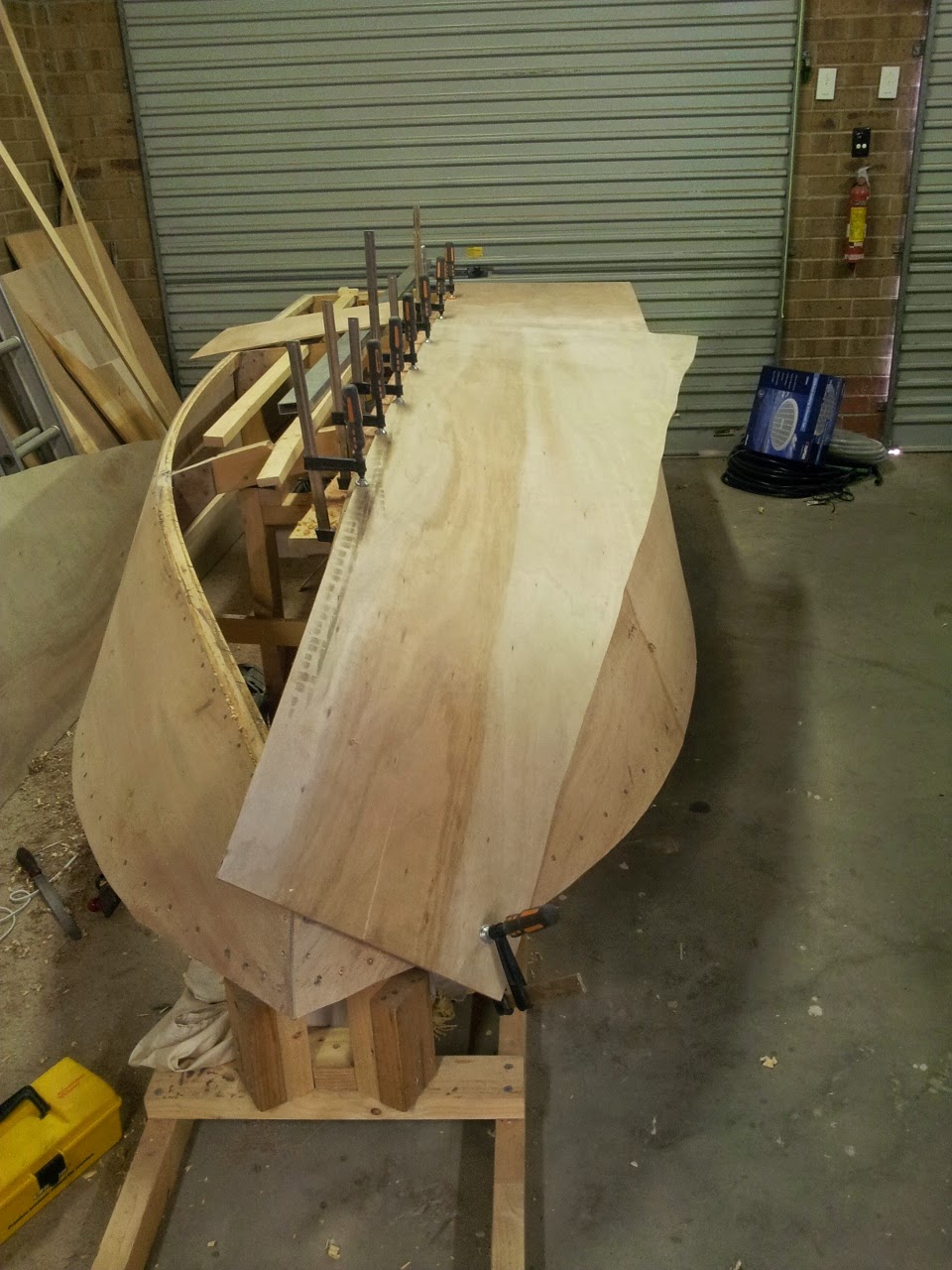.jpg) |
Rough fitting the bottom planking |
One of the major steps to be completed was the fairing of the keel, battens, chine and stem. It was a trial and error process to get the right curves near the bow of the boat. In the photo below, small plywood panels are being used to determine where material needs to be removed and how much.
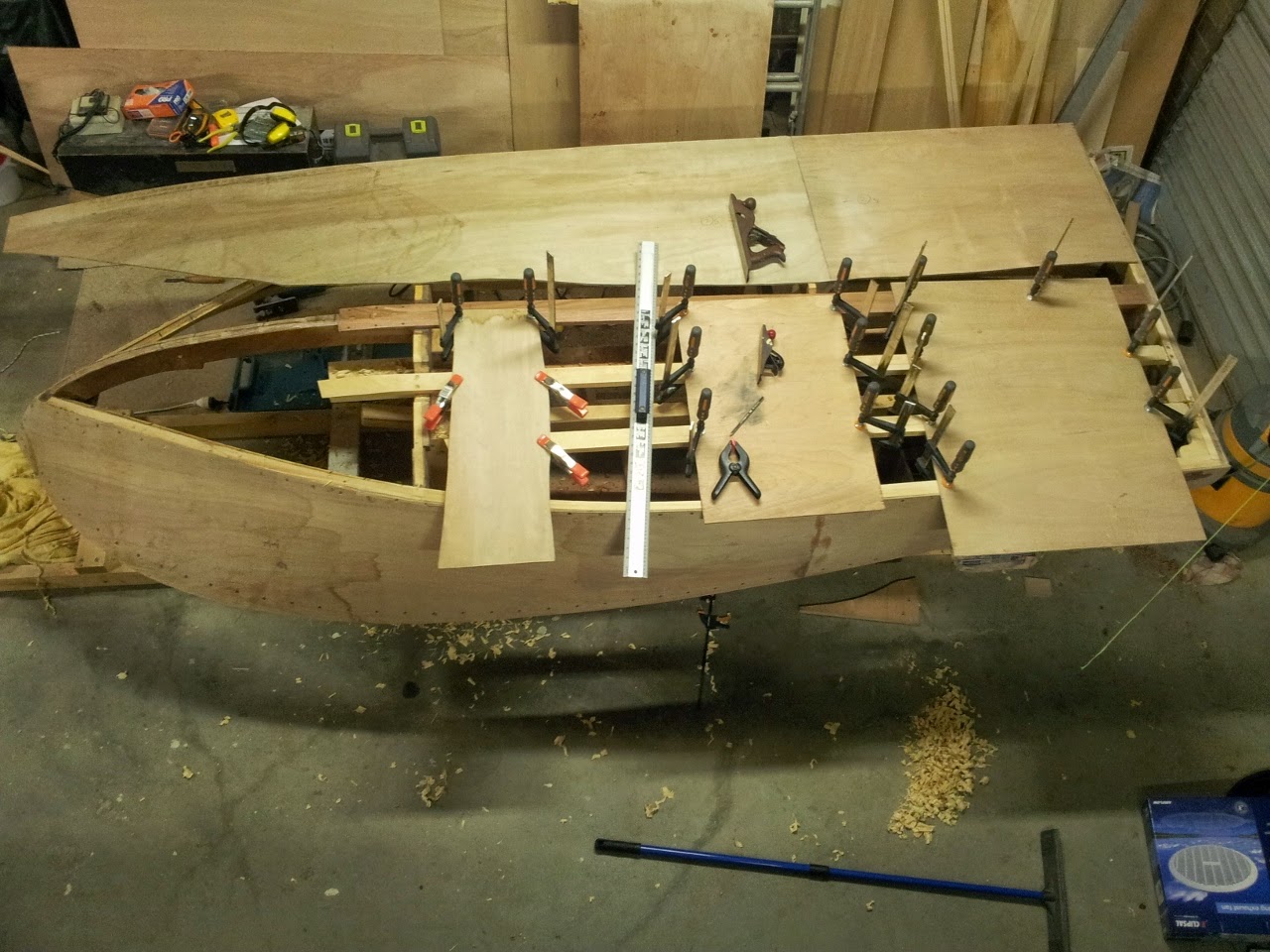.jpg) |
Determining where to remove material during fairing |
The ends of the battens were particularly challenging. I got blisters on my hands planing them down to a taper. There was a lot of trial and error getting it right.
With the planking clamped to the keel and my amenable family members holding the plywood against the chine, I climbed repeatedly under the boat to observe where material needed to be removed from the battens. The plywood then being removed, the battens were planed to shape and the process was repeated. I didnt get it perfect but I am convinced the fit is good enough.
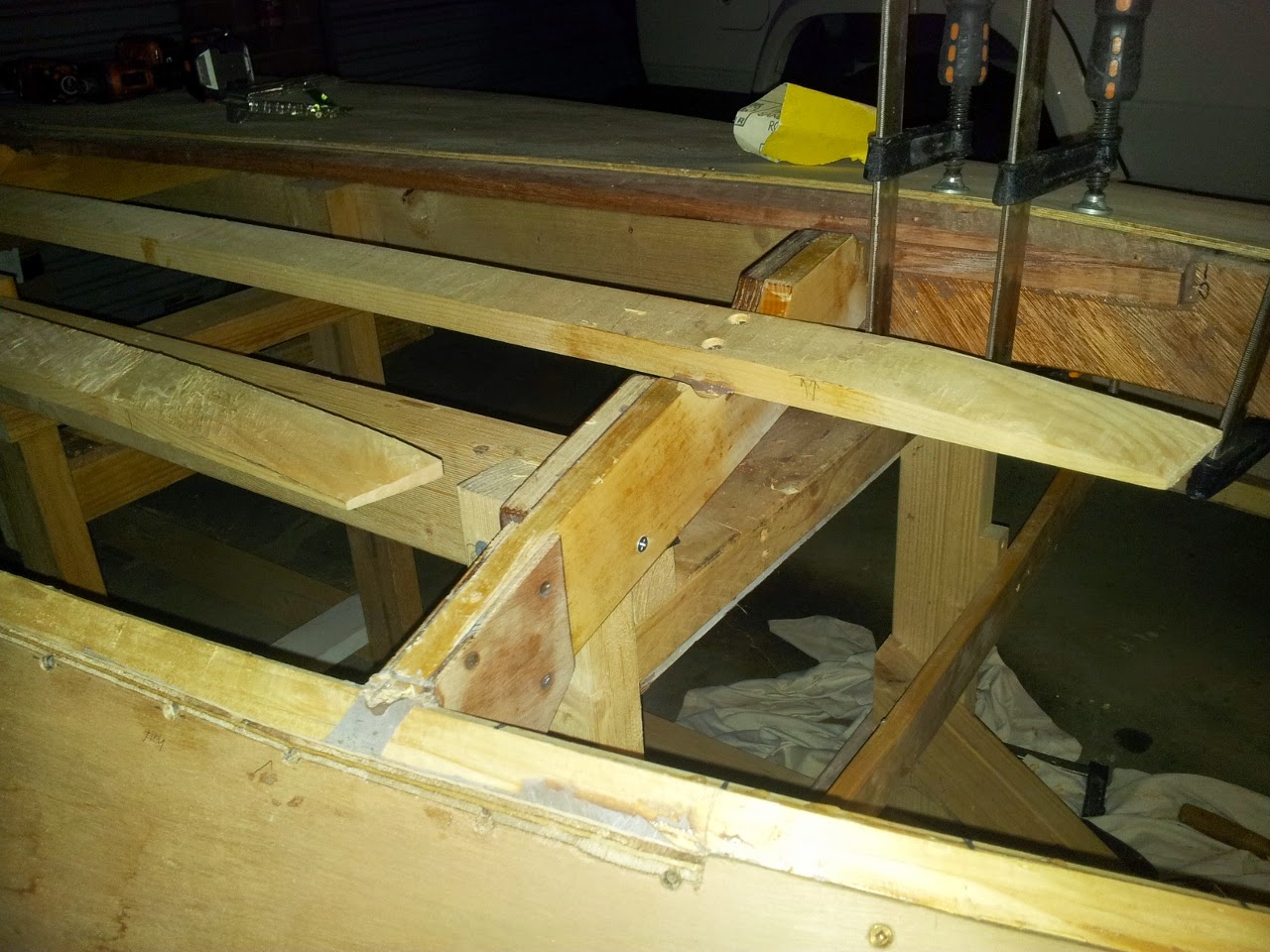.jpg) |
Fairing the batten ends |
The tools used for fairing included a block plane, a rebate plane, a rasp, chisels, sanding boards and good old sand paper. The most useful tools by far were the planes. I briefly tried using a power plane but quickly gave up as it was simply too unwieldy.
.jpg) |
Fairing tools |
Initially, I was really struggling with fairing the hardwood kapur keel. I had resorted to vigorously sanding with my sanding boards to obtain the correct angle on the keel. This was working ok, but it was incredibly labor intensive.
It was then that I made the brilliant decision to properly sharpen by plane blades.
I can't emphasise enough how much difference razor sharp plane blades make!!
Do yourself a massive favor and sharpen your tools!!
(probably everyone goes through this realisation at some time in their life)
After sharpening the blades, the kapur keel became like butter and the fairing became a delicious dream.
I received 3 whetstones for my birthday along with a honing guide. The epoxy deadens the blades fairly quickly but keeping the blades sharp makes fairing very quick and easy.
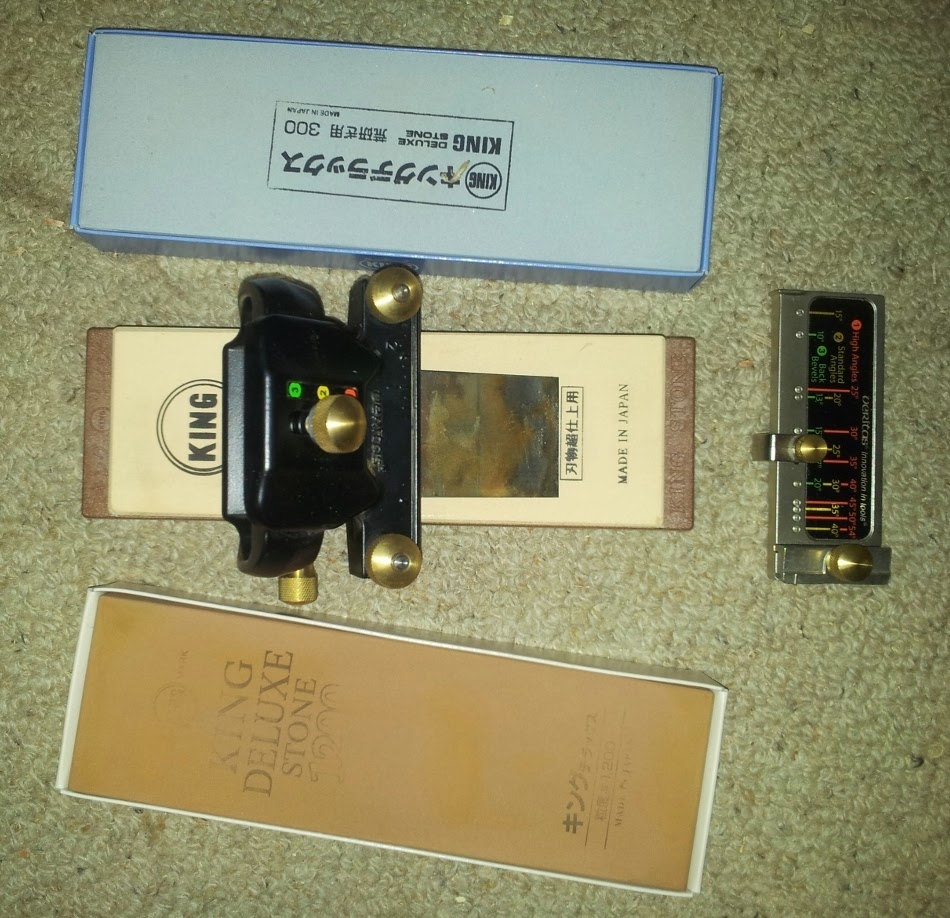.jpg) |
Japanese Whetstones - from top - 300 grit, 6000 grit & 1200 grit |
Once the keel, battens and chines were faired, I worked on creating the butt joint between the side and bottom planking near to the bow. Carbon paper was very useful for determining at which point to trim the bottom planking. Working along the chine towards the stem, I completed the butt joint by marking with carbon paper; trimming with a jigsaw; and finishing the joint with a hand plane. It required quite a bit of trial and error but I am very happy with the result.
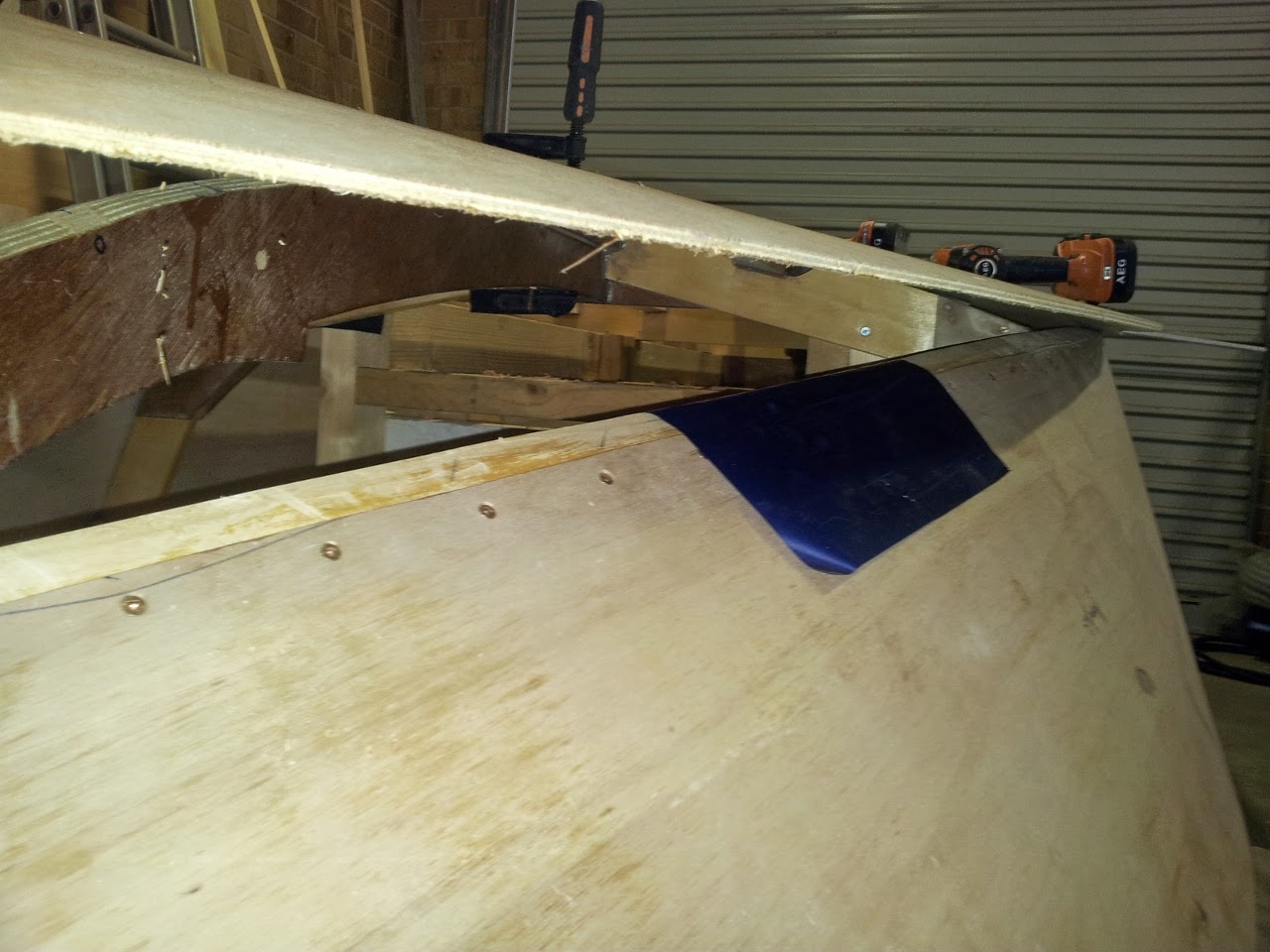.jpg) |
Using carbon paper to mark the butt point position on the bottom planking |
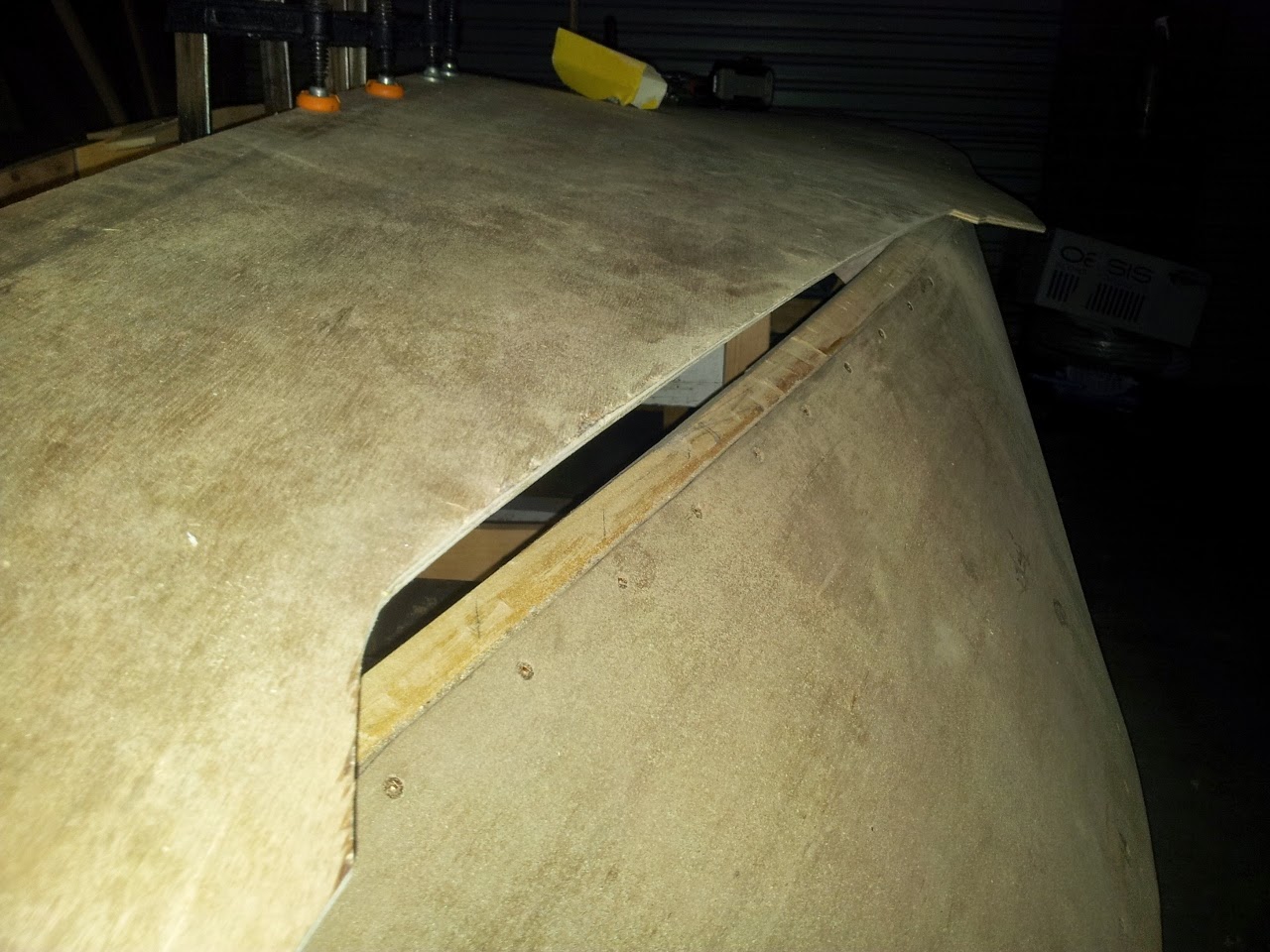.jpg) |
Half way through creating the butt joint along the chine at the bow |
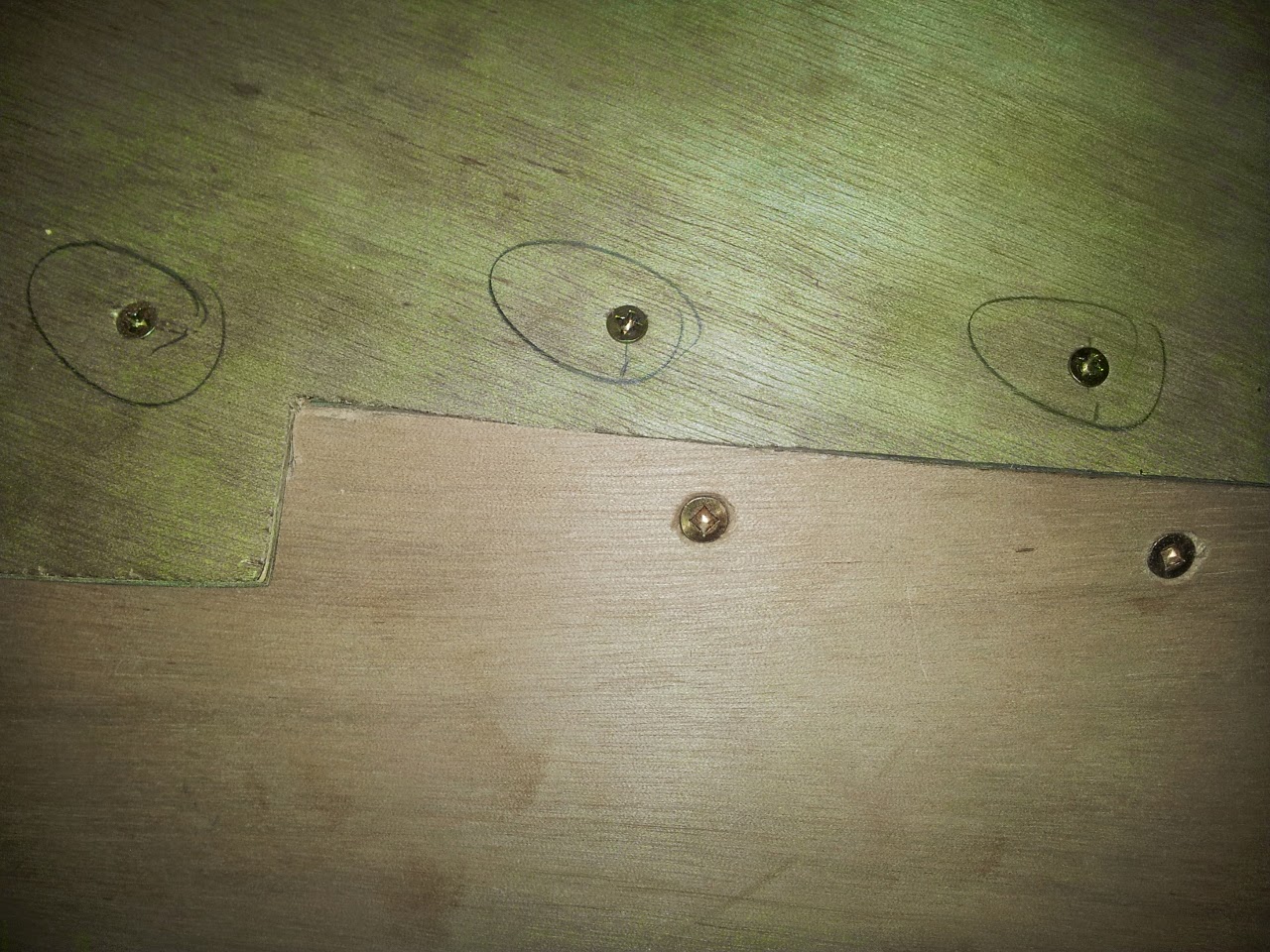.jpg) |
Transition joint - lap joint to butt joint. |
A rough fit of the bottom planking was carried out using 6 gauge self drilling wood screws. As with the side paneling, these screws provided a pilot hole for the 8 gauge silicon bronze screws used in the final application.
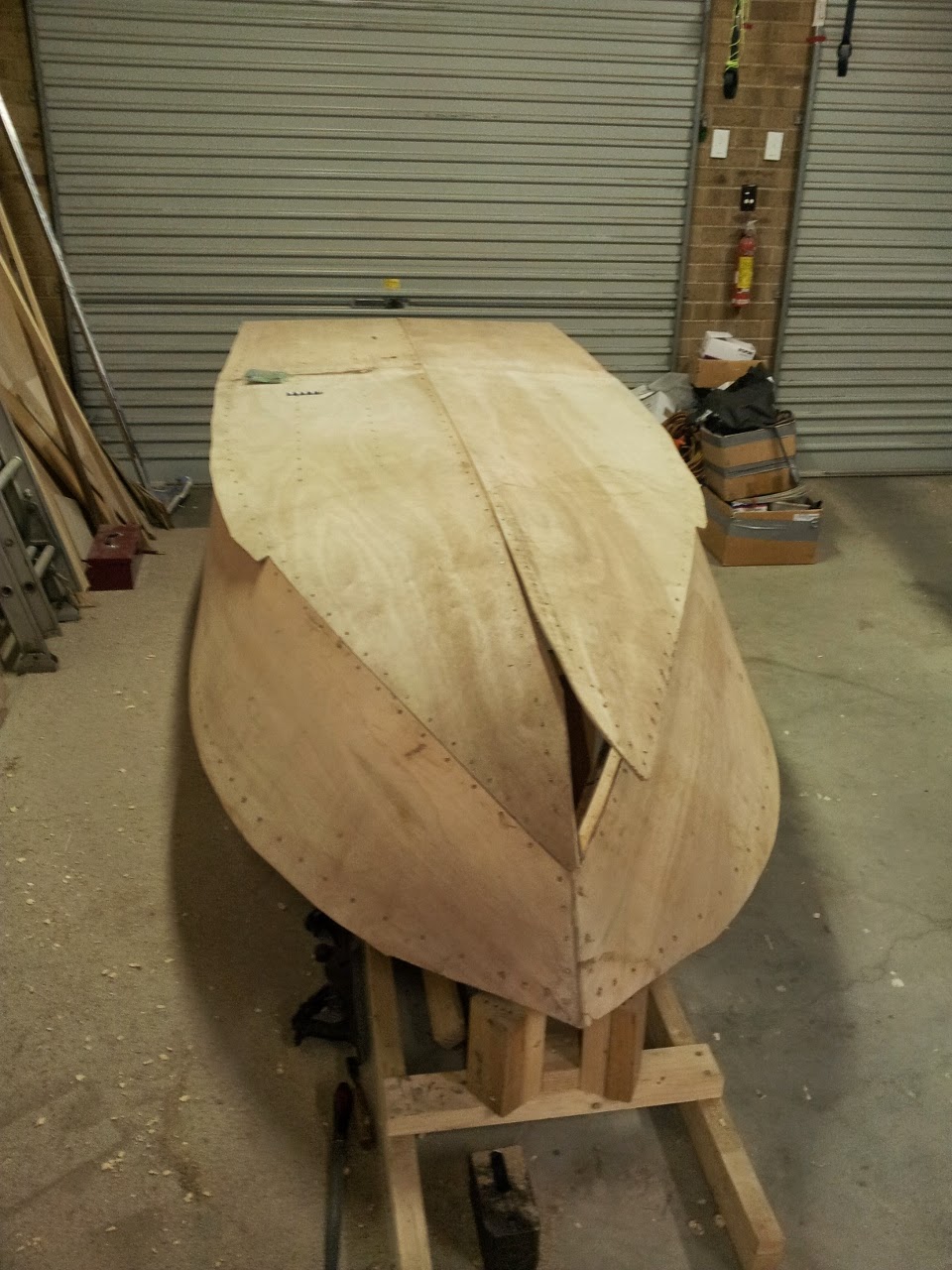.jpg) |
Rough fitting the bottom planking |
The plywood paneling edges were angled slightly with a plane to achieve a good butt joint along the keel. The meeting point of the two plywood panels at the stem required some careful work. Halfway along the stem there is a transition joint where the bottom planking goes from butt jointing to lap jointing. The butt jointing required some careful work with the rebate plane to get it accurate.
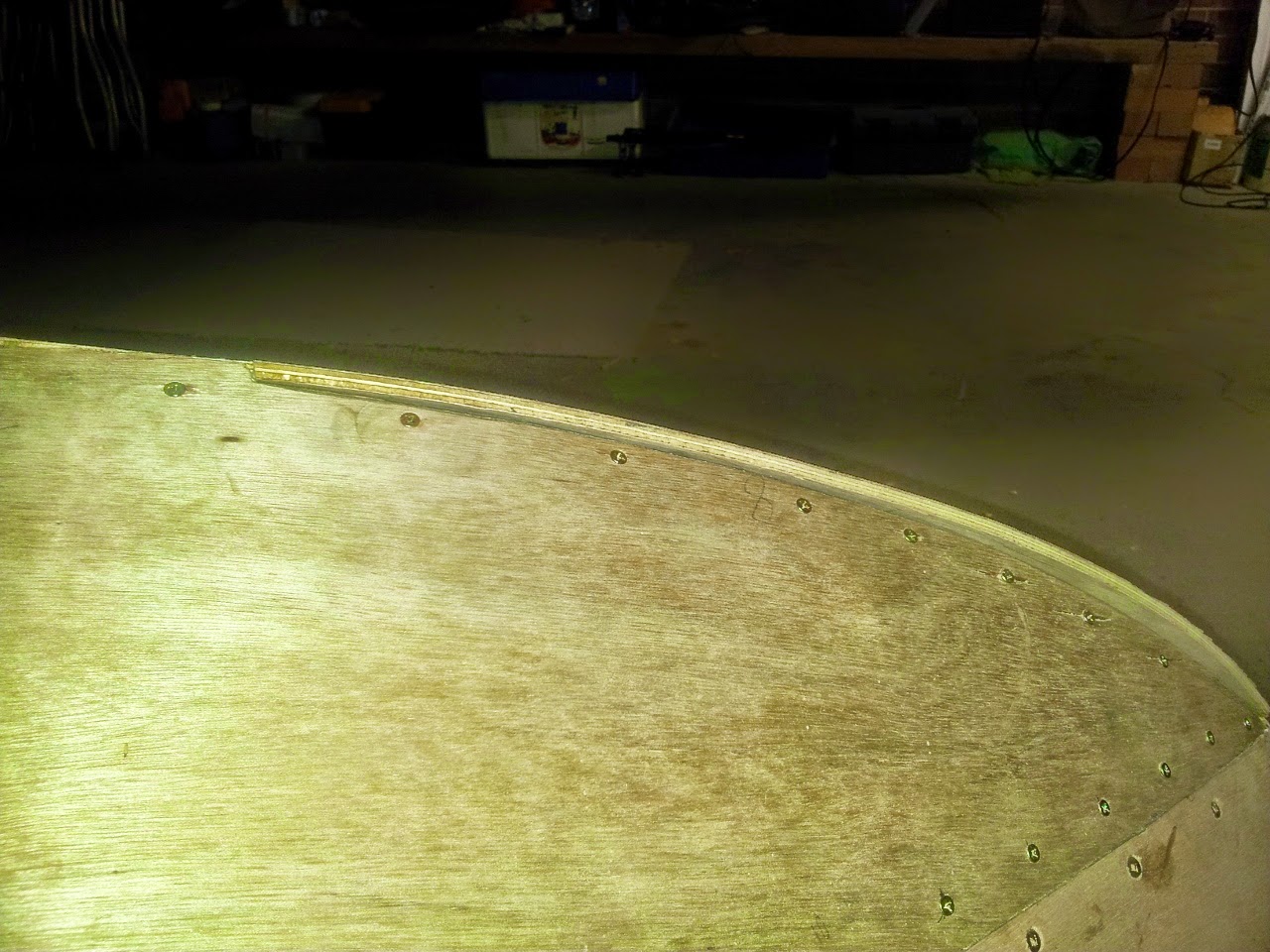.jpg) |
Transition joint between bottom panels at stem. |
The plans require installation of knees at the transom-chine junction. These were made out of plywood and the transom angle on the knees were cut on the scroll saw. The size of the limbers was increased to ensure that water will freely flow without the limbers getting clogged up with various, filthy, river water debris.
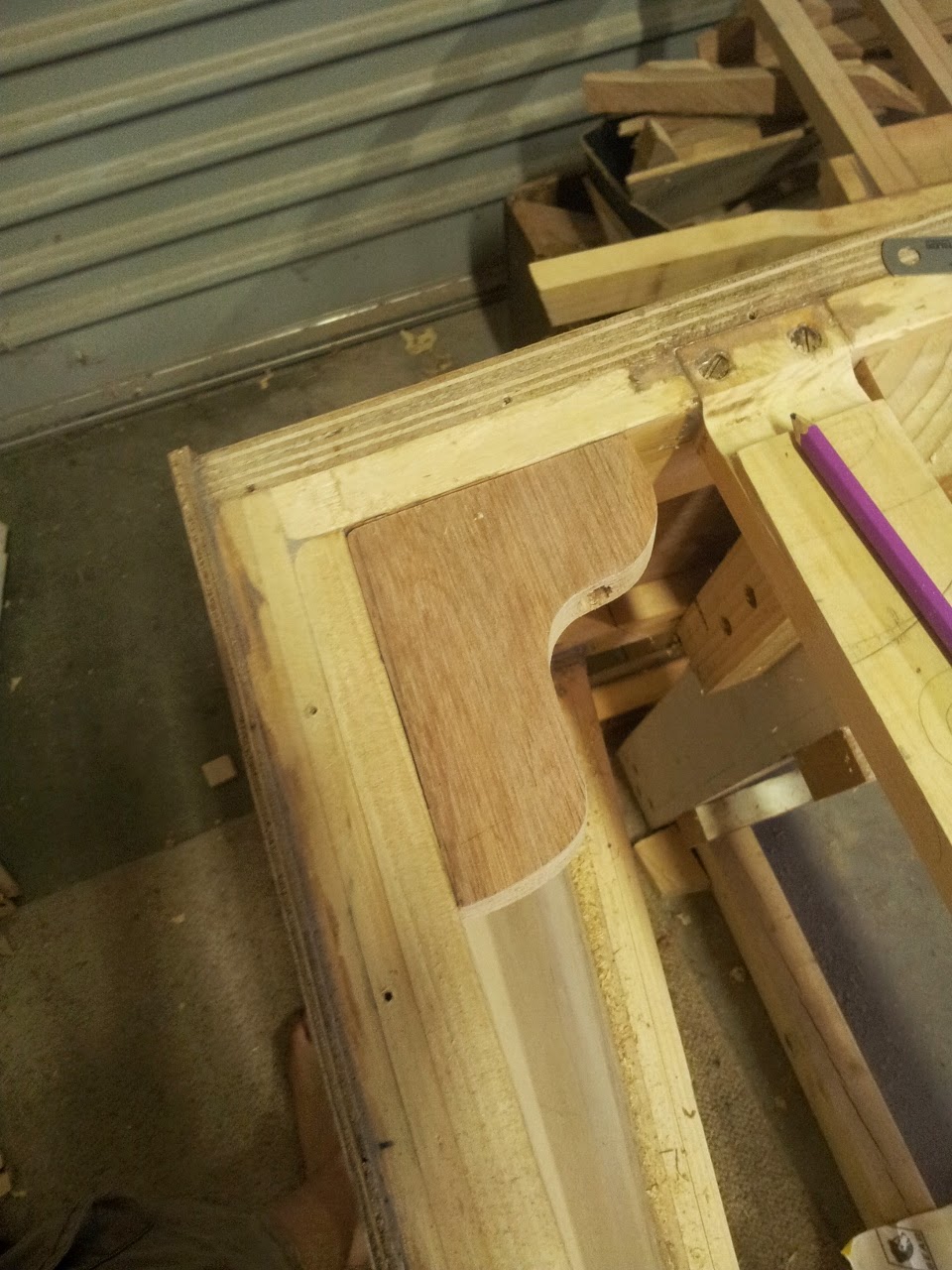.jpg) |
Installation of transom-chine knees & enlarged limbers |
Before the final glue-up, the internal surfaces of the limbers were coated with epoxy as this would be very difficult to do once the bottom planking is installed.
A 5mm lamination of kapur was added to the keel to bring it to 25mm thick as specified in the plans. 20mm probably would have been ok; however to my eye it looked too small and I would have been forever annoyed and bothered that it was not 25mm.
25mm it now is and I am a happy man!
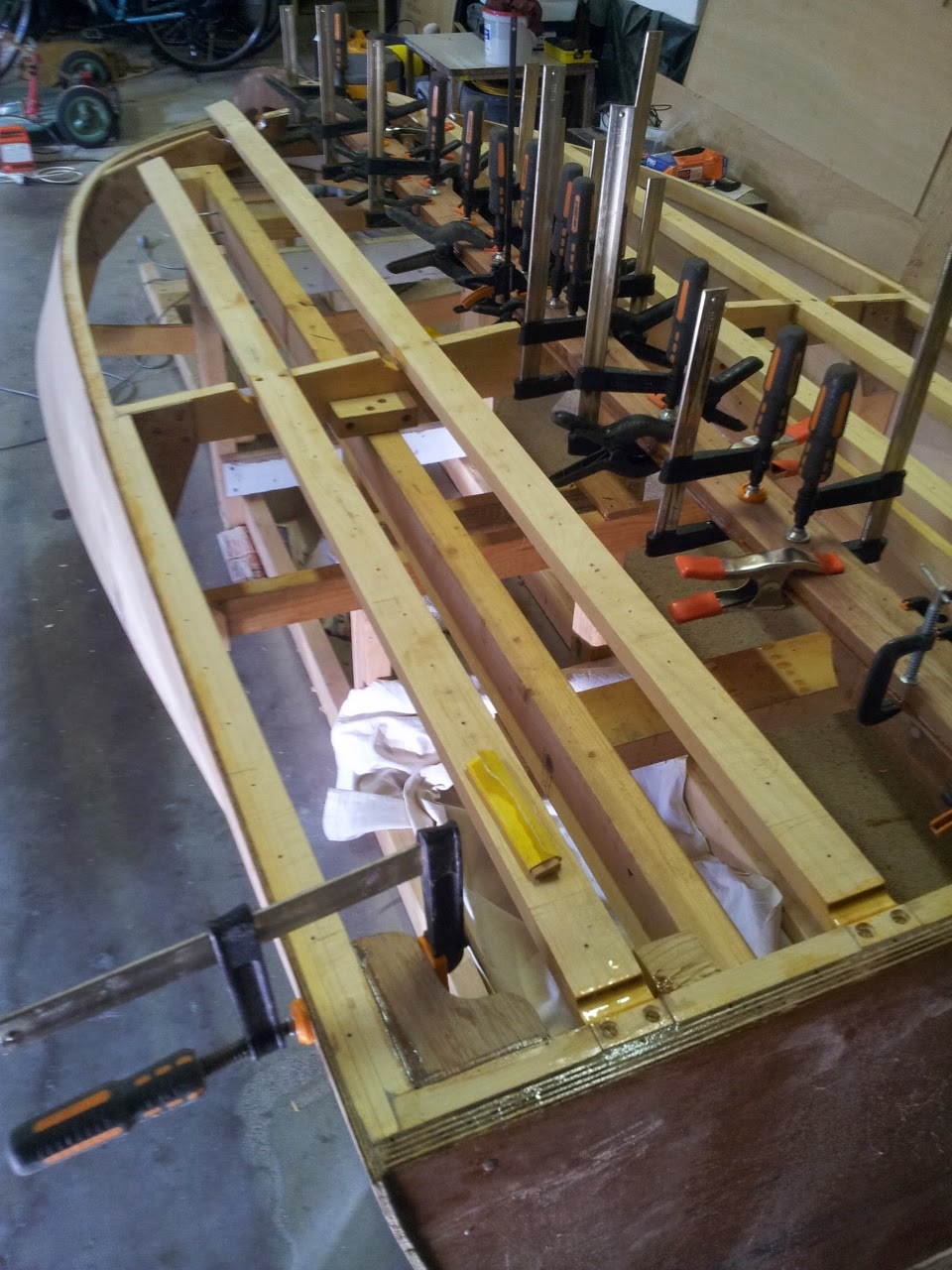.jpg) |
Gluing the keel lamination, gluing transom-chine knees and coating limbers. |
The screw holes in the bottom panel were countersunk on the drill press (the holes in the centre of the board were done with the hand drill due to insufficient depth in the drill press table.)
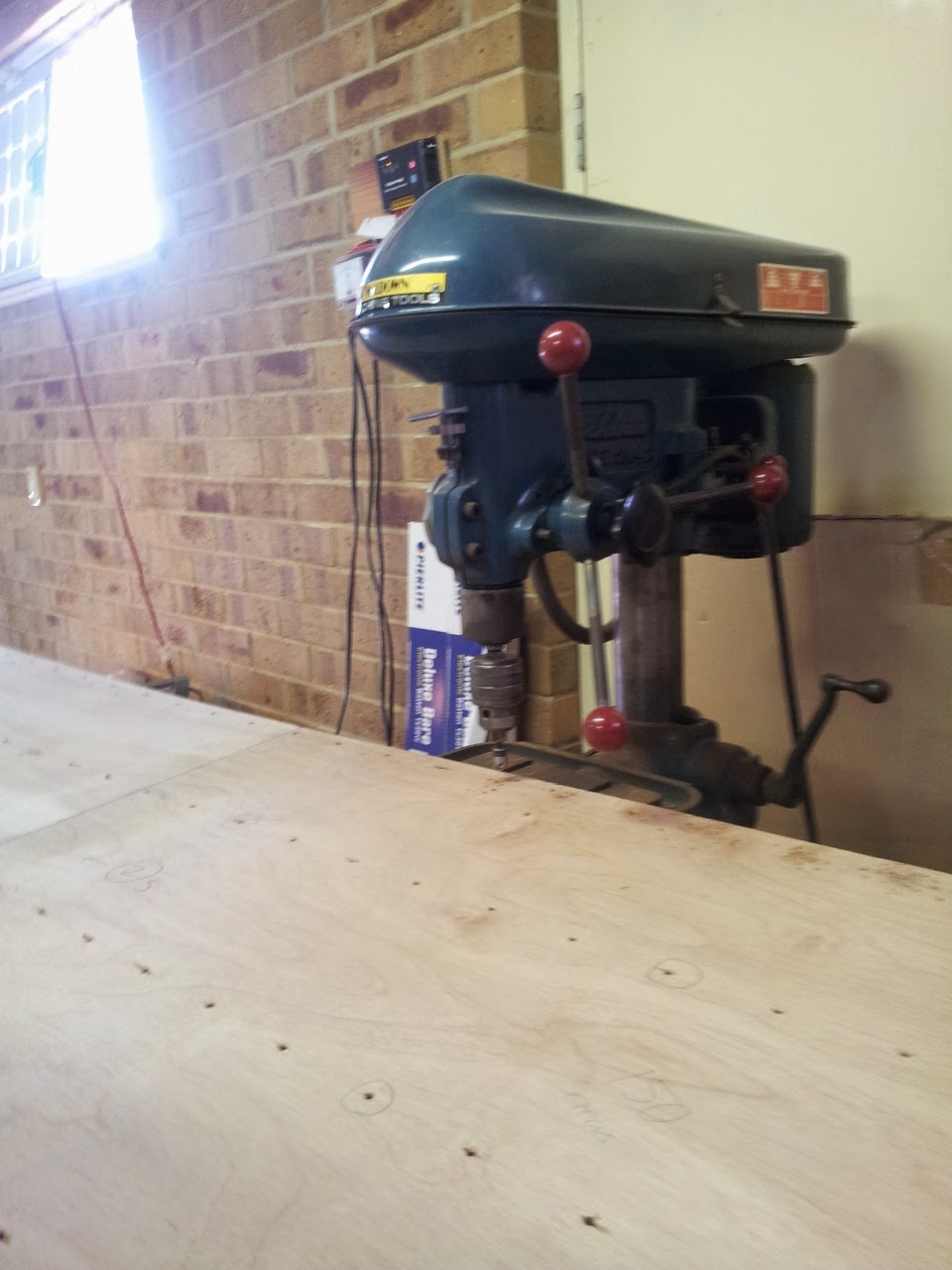.jpg) |
Countersinking holes in bottom planking |
All surfaces to be glued were thoroughly sanded and vacuumed before the application of epoxy. As with the side planking, all surfaces were given an initial coat of epoxy and left for an hour or so to allow the epoxy to seep into the timber.
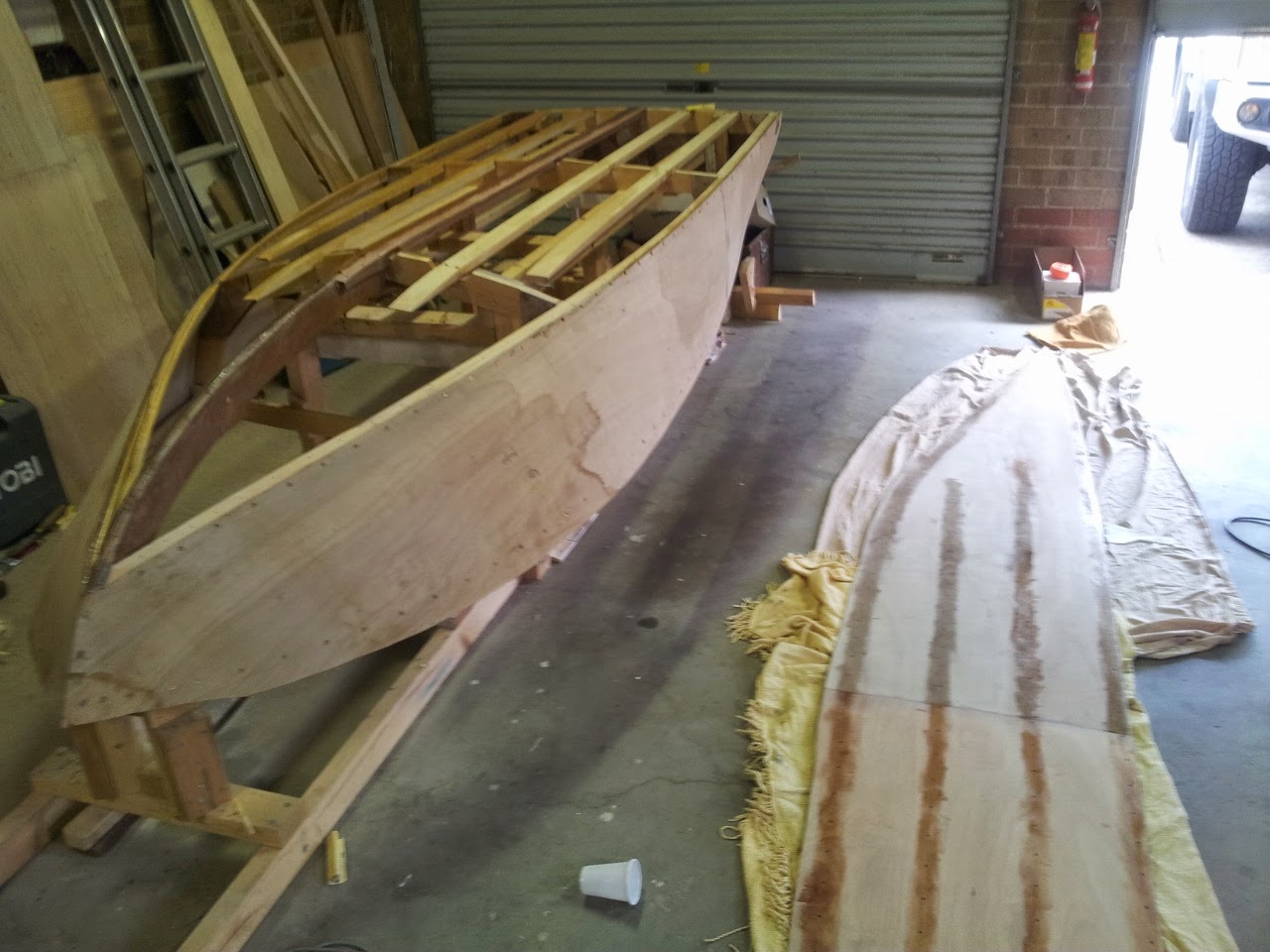.jpg) |
Pre-coating with epoxy |
Thickened epoxy was spread liberally on all the joint surfaces and the panel was screwed in place with 144 screws.
All the excess epoxy was scraped away while it was soft. This will make my job a lot easier later on. Adding extra height to the building form was a brilliant idea as I have been frequently climbing under the boat and it is difficult enough as it is!
The final result is that half the bottom paneling is installed!
If I got all my friends together and we all sat on the port shear, the boat would probably float! But I think I'll just wait till friday when I plan to have both bottom panels glued on. Actually, I think I'll finish the boat completely before placing in the water!
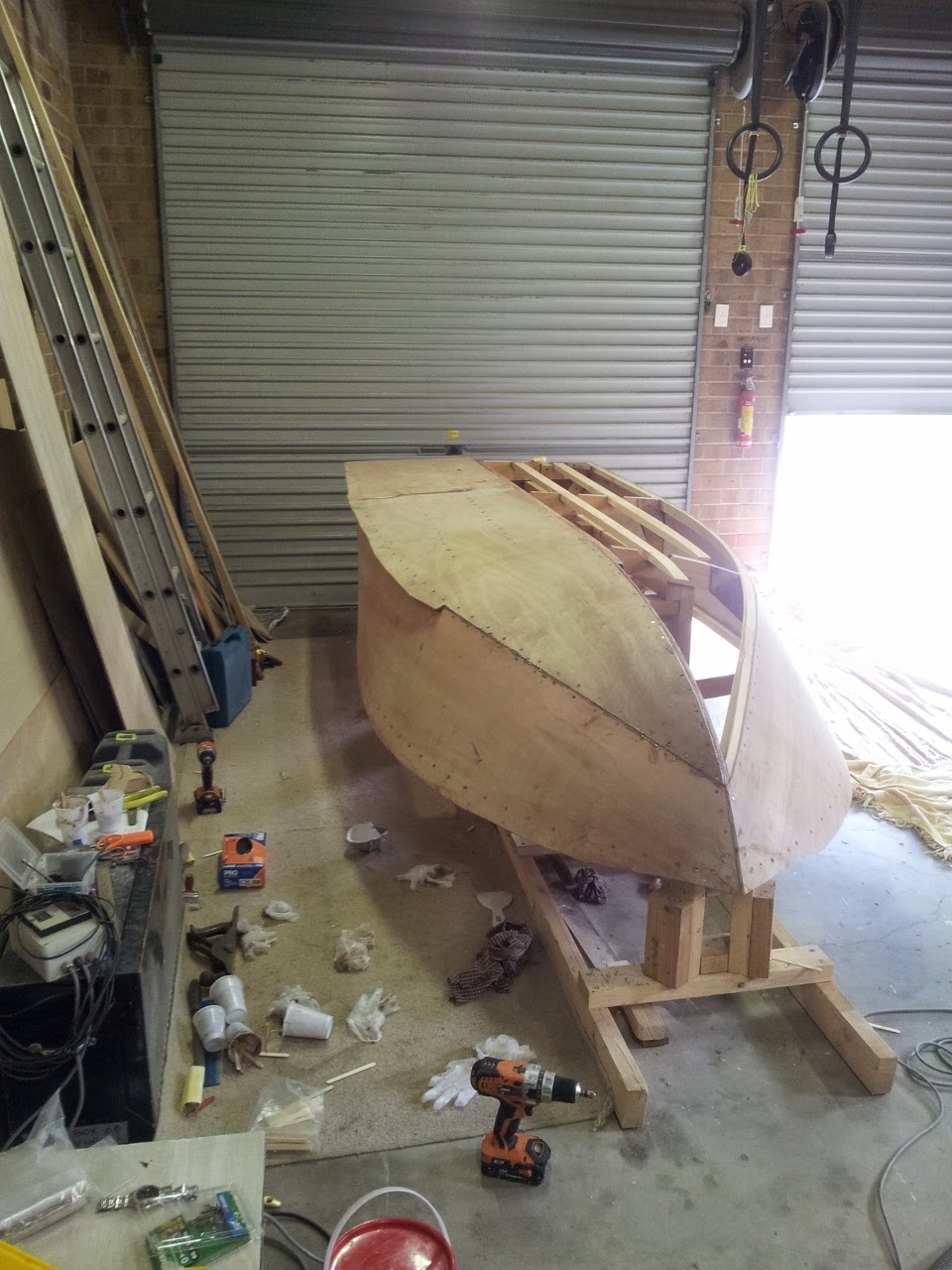.jpg) |
Plywood panel glued in place |
The weather is getting colder already and I have a busy schedule ahead of me this year. I am not sure how much I'll get done over the winter but for now I have achieved my objective of getting the bottom of the boat glued on (provided I get the other half glued on this week).
Till next time reader.